People in the eyewear industry recognize that ISO 12870 is the most authoritative and widely used test standard for spectacle frames. It formulates the specific test requirements and test methods for the spectacle frame in detail. Based on ISO 12870, standards organizations and institutions around the world have derived different versions on this basis, such as ANSI Z80.5 in the United States and GB/T 14214 in China. Today, we will take you a general understanding of this standard so that you can easily understand and apply it better.
Where to Get an ISO 12870: 2016 Standard Free of Charge?
Please click HERE to view the complete standard of ISO 12870: 2016 in PDF, and you are allowed to download it. You can also directly reach AMADE TECH to attain one.
What Types of Spectacle Frames does ISO 12870 Apply to?
ISO 12870 is applicable to all spectacle frames types, such as:
- Rimless frames
- Semi-rimless frames
- Folding spectacle frames
- Ones made from natural organic materials
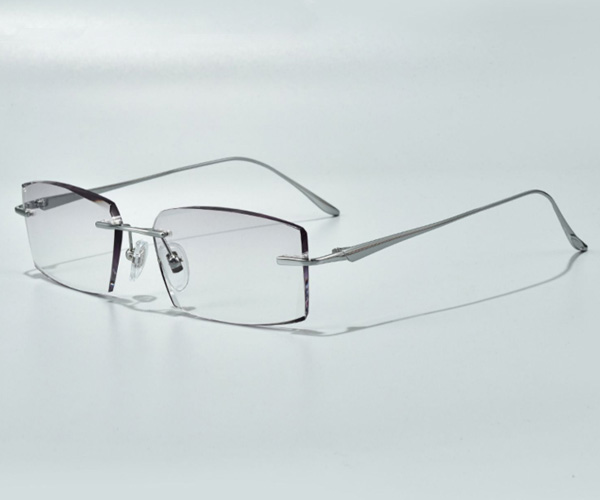
Rimless frame
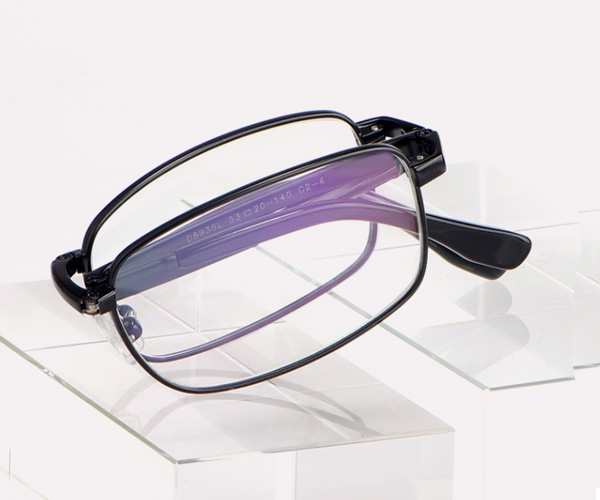
Folding spectacle frame
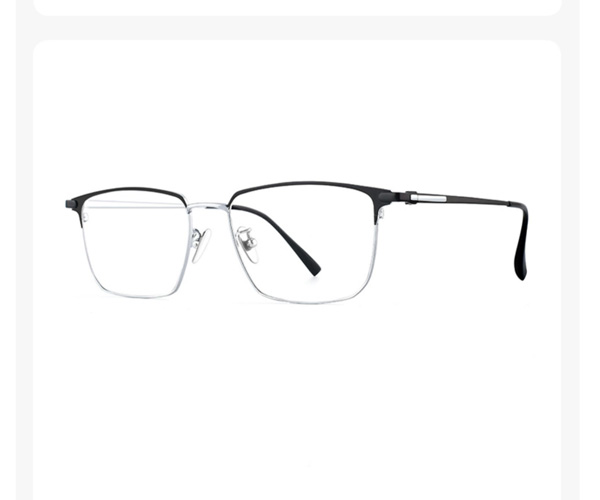
Semi-rimless frame
Notes: Complete custom-made spectacle frames and frames designed specially to provide personal eye protection are not included.
What Are the Mandatory Requirements and Tests Stipulated in ISO 12870?
The following requirements are mandatory for all frame types to which this standard applies:
1 Construction
Areas of the spectacle frame that is in contact with the wearer are required to be smooth, without sharp protuberances, and all edges should be rounded.
2 General physiological compatibility
It requires that the spectacle frames have no adverse influence on the health and safety of the wearer. In particular, the choice of materials is crucial. They are the source of the safety of the finished products.
3 Tolerance on screw threads
Refer to ISO 11381 for the tolerance of the crew threads used in the spectacle frame.
4 Dimensional stability at elevated temperature
The frame sample with test lenses placed on the flat plate is placed in an oven being exposed to a relatively constant temperature of (55±5)°C for 2 hours. The distances between the side tips before and after heating are measured and recorded according to a predetermined procedure.
It requires that the distance can’t vary by more than + 6 mm or – 12 mm. And for small spectacle frames (The tip of the side is less than 100 mm from the backplane of the front), the tolerances are reduced to + 5 mm or – 10 mm.
5 Resistance to perspiration
The lowest part of the frame sample with the test lenses is positioned not more than 12 mm above the artificial sweat solution. The solution is heated and maintained at (55±5)°C. After 8 h ± 30 min, the test sample is visually checked by comparison with the same untested frame.
Except for joints and screws, it requires no spotting or colour change ( excluding loss of gloss) anywhere on the frame.
Then the test sample is replaced and exposed to the above sweat environment at (55±5)°C for a further 16 h ± 30 min. The same inspection method as above is used to check.
Corrosion, surface degradation or separation of any coating layer on the parts liable to come into prolonged contact with the skin during wear is unacceptable.
6 Mechanical stability
Mechanical stability comprises 3 items: Bridge deformation, lens retention characteristics and endurance.
Both bridge deformation testing and lens retention characteristic testing share a test method. One lens of the test sample is fixed. The other lens is pressed against a pressure peg with an increasing force until a maximum of 5 N or prescribed displacement is attained and kept for 5 seconds. After a relaxation period of 20 s, the pressure peg is lowered again until it just rests on the lens to measure and calculate the deformation and percentage deformation.
For bridge deformation testing, the frame sample shall not fracture and crack at any point, or the percentage deformation shall be less than 2%.
For lens retention testing, the test lens cannot dislodge from its original location in the groove or mount.
Endurance
The nose bridge of the frame sample is restricted on a bridge support. One frame side tip is fixed. The other one is clamped in a rotatable clamping device to cause the side tip to make a cyclical rotating movement in a prescribed path. After a total of 500 cycles at a rate of 40 CPM, the difference in distance between 2 frame sides before and after the test is measured and calculated.
The permanent deformation should be not more than 5 mm.
Fracture at any point is not allowed.
Force more than light finger pressure to open and close the sides is not allowed (except for ones with sprung joints).
Closing of either side under its own weight at any point is not allowed (except for ones with sprung joints).
7 Resistance to ignition
One end of the steel rod is heated to (650±20)°C. The heated end surface is pressed downwards and vertically against the surface of the test sample with the rod’s own weight for a period of (5±0.5) s. Visual inspection is conducted during the test.
It requires no continued combustion of the test sample after the withdrawal of the test rod.
The following mandatory requirements are for frames other than rimless and semi-rimless frames:
Measurement system & Dimensional tolerances on the nominal size
For the measurement system and boxed lens measurement method, please refer to ISO 8624
Tolerances applied to the marked dimensions of the unglazed frame using the boxed lens measurement method as below:
1) Horizontal boxed lens size: ± 0.5 mm
2) Distance between lenses: ± 0.5 mm
3) Overall length of side: ± 2.0 mm
How Many Test Samples are Required for the Spectacle Frame Testing?
You are required to select specimens of each spectacle frame model at random, then number them sample 1 and sample 2, respectively.
In addition, 2 more samples are required if you perform nickel release testing.
How to Condition the Samples and What Is the Ambient Temperature for the Test?
You need to condition the samples at an ambient temperature of (23±5)°C for at least 4 hours before testing. Usually, the temperature of a standard constant temperature laboratory is just enough to meet this requirement.
The ambient temperature for a series of tests is consistent with the above condition.
What Is the Test Sequence?
What Core Test Machines Are Needed for Performing ISO 12870 Test Items?
Conclusion
The above is only a summary of some of the contents of ISO 12870 but not all. If you want more details, please refer directly to the standard. If you are looking for related equipment or have any questions about the devices required by this test standard, please contact us for assistance.