UV Aging Test Chamber China Supplier and Manufacturer
UV Accelerated Weathering Tester is a laboratory environmental chamber designed to simulate and speed up the effects of sunlight exposure, temperature, humidity, and other weathering factors on materials.
The UV aging test chamber is applicable to various industries, including automotive, aerospace, coatings, plastics, textiles, and construction. It is used to assess the weathering resistance of materials, such as paints, coatings, polymers, plastics, textiles, rubbers, adhesives, composites, etc. The test results help manufacturers optimize formulations, select suitable materials, and ensure product quality and longevity.
Test Principle
The sample is mounted in the test chamber and exposed to the simulated ultraviolet light of specified irradiance emitted from the standard fluorescent ultraviolet lamp (UVA-340 or UVB-313). In addition, more weathering conditions such as rain, high temperature, high humidity, condensation, and darkness in the natural climate can be simulated and added to form a desired test cycle and act on the sample under the specified conditions. The sample is examined for changes after subjecting to alternate test conditions for a given period.
The change in physical or chemical properties of the material during a few days or months in the UV test chamber is equivalent to that caused over months or years in the natural environment, so the sample’s ability to resist fading, discoloration, tarnish, powdering, cracking, turbidity, bubbling, embrittlement, recession, and oxidization can be obtained with the UV test chamber in a relatively short period of time.
AmadeTech ultraviolet accelerated weathering tester consists of a chamber made of UV-resistant stainless steel, a temperature control system, a spray system, and an interactive system.
Four on each side, a total of 8 fluorescent ultraviolet lamp tubes (UVA-340 or UVB-313) are adopted as the light source, arranged horizontally and equidistantly in parallel on both sides of the test area inside the chamber. They emit ultraviolet radiation similar to sunlight during the test. Removable sample holding walls made of stainless or aluminum next to the lamp tubes on both sides can fix the sheet samples and expose them evenly to irradiation.
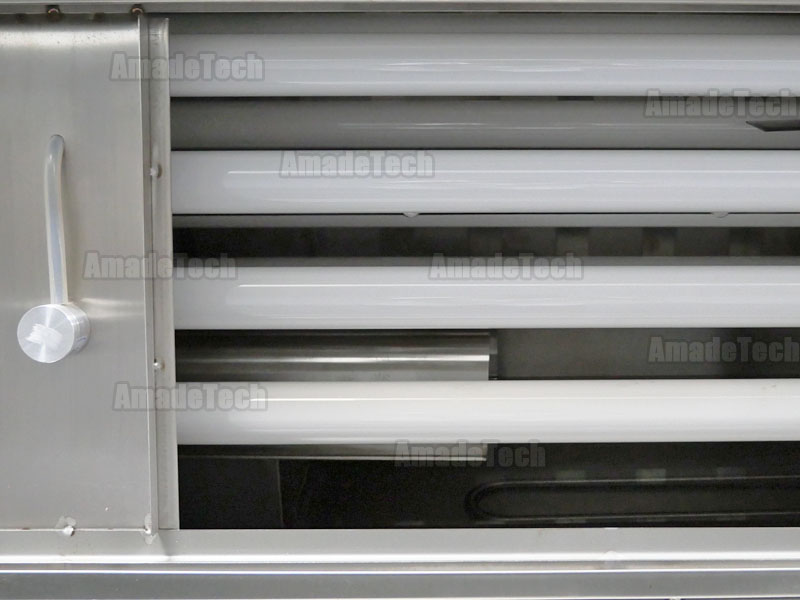
Fluorescent tubes
Several water nozzles are arranged behind the lamp tubes. They can spray water under control through the gap between the lamp tubes to subject the samples to rainfall. There is a sink below the two rows of lamps. It has a heating unit and temperature-monitoring components. Water is automatically pumped here and heated to obtain the desired test temperature and generate steam to form dew on the sample through moisture condensation.
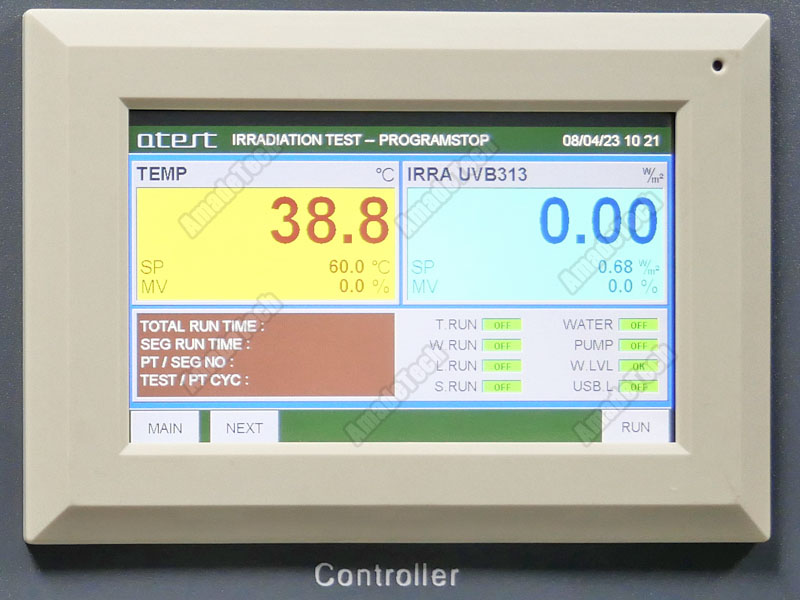
Touchscreen controller
This UV test chamber has a set of sensors and controls to monitor and regulate temperature, UV intensity, and other parameters. For example, solar eyes and black panels are available to monitor the irradiance intensity and chamber temperature. The machine supports three different test modes: irradiation, spray, and condensation. You can set each mode’s time, temperature, irradiation value, and other parameters individually. In addition to the fixation control mode, you can also use the program control mode: it supports custom combinations of test modes with different parameters in different orders to get an anticipated test program, and a program supports up to 30 segments in a cycle. After the test is completed, the machine stops automatically.
Test Standards
- ISO 11507 Paints and varnished – Exposure of coatings to artificial weathering – exposure to fluorescent UV lamps and water
- ISO 4892-1 Plastics-methods of exposure to laboratory light sources-Part 1: General Guidance
- ISO 4892-3 Methods of exposure to laboratory light sources-Part 3: Fluorescent UV lamps
- ASTM D 4587 Standard practice for Fluorescent UV-Condensation exposures of paint and related coatings
- ASTM D 4329 Standard practice for fluorescent UV exposure of plastic
- ASTM G 151 Standard practice for exposing nonmetallic materials in accelerated test devices that use laboratory light sources
- ASTM G 154 Standard practice for operating fluorescent light apparatus for UV exposure of non-metallic materials
- BS 2782 Part 5 Method 540B methods of exposure to lab light sources
- SAE J2020 Accelerated exposure of automotive to Lab light sources
- JIS D 0205 Test method of weather-ability for automotive parts
To accommodate samples of irregular shapes and dimensions, AmadeTech also can supply UV test chambers with shelves to place the samples and the lamp tubes are located on the ceiling of the inner chamber. Please refer to the figure below:
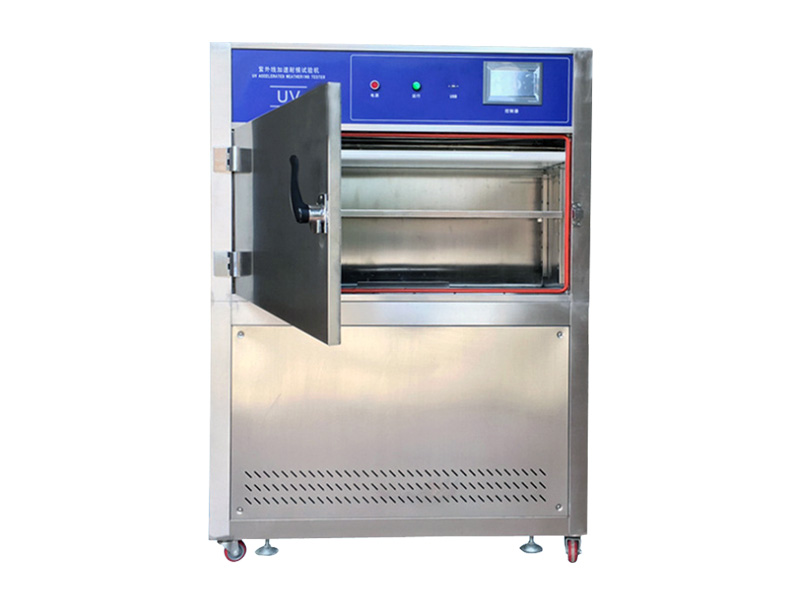
Technical Parameters
Model | AT-C1002 series |
Light Source | UV-A (Wave length 340 nm) |
UV-B (wave length 313 nm) | |
40 W – 8 pieces (Service life: up to 5000 hours) | |
Irradiance Range | 0.3 W / m² ~ 1.55 W / m² |
Black Panel Temperature (BPT) | RT + 10 ℃ ~ 80 ℃ |
Main Material | Stainless steel SUS 304 |
UV Weathering Test Chamber | Effective irradiation area: 1020 × 290 (mm) |
Exposure ways: illumination, condensation and water spray in combinations, and the cycle order is adjustable | |
Sample Rack | 75 × 300 (mm) – 24 pieces (for Standard specimens) |
75 × 150 (mm) – 48 pieces (for Standard specimens) | |
Please specify for other non-standard sample racks | |
Materials of racks: Stainless steel or aluminum alloy | |
Controller | Touchscreen |
Communication Mode | RS232 |
Water Consumption | Use purified water or distilled water |
Appr. 4 Litre / minute (Spray) | |
Appr. 7 Litre / day (Condensation) | |
Overall Dimensions | 1300 × 550 x 1480 (mm) |
Power | AC 220V +/- 10 %, 50 / 60 Hz, 3 kW or AC 110 V |
UV Weathering Test Chamber Features
- Rigid housing is formed from precision 304 stainless steel sheets.
- Equipped with the special 40W UV lamp tubes(UVA-340 or UVB-313) with 2 columns of 8 pcs to provide stable light source.
- Original UVA or UVB lamps from Q-LAB USA are adopted to ensure the repeatability and reproducibility of testing results.
- A black panel thermometer monitors the temperature and solar eyes monitor the intensity of irradiation.
- Fitted with the touch screen to set parameters and control the test conveniently.
- The specimen racks are made of rugged stainless steel or aluminum alloy with corrosion resistance.
- The USB interface allows the operator to export all test data by U disk or RS 232 for communication.
- Water tank can be filled automatically in case of dry burning.
- The spray system allows intermittent or continuous spraying.
- This machine can replicate variously alternate weathring conditions, including UV radiation, water spraying, condensation, high temperature, darkness in combinations.
- Considerate safety devices are available, including ground protection, water shortage protection, over-temperature protection, overload protection, short-circuit protection, etc.
- Casters at the bottom of the test machine are for convenient mobility.
FAQs
A UV accelerated weathering tester is a specialized testing device to simulate and accelerate the effects of sunlight exposure and other weathering factors on material. It creates an artificial environment that replicates the damaging effects of sunlight, temperature, humidity, and due on materials, allowing researchers and manufacturers to assess the durability, performance, and lifespan of various materials under controlled conditions.
By subjecting materials to accelerated weathering conditions, the tester helps evaluate their resistance to fading, discoloration, cracking, peeling, degradation, and other forms of deterioration that occur due to long-term exposure to outdoor environments. The results obtained from the UV accelerated weathering tester assist in the development, optimization, and quality control of materials used in lots of industries.
Time Efficiency
We know that Ultraviolet light only accounts for 7% of the total sunlight, but it plays a core role in the deterioration of outdoor materials. UV weathering test is an essential measure for people to research and know the degradation state of specimens in advance as time goes on. The tester accelerates the degradation process of materials, allowing manufacturers to evaluate their performance and durability in a shorter time frame. This saves significant time compared to natural weathering tests, which could take months or even years to obtain comparable results.
Cost Saving
By reducing the testing time, manufacturers can save costs associated with extended product development cycles and field testing. It enables them to identify potential issues or weaknesses in materials early on, leading to cost-effective improvements and avoiding costly failures in real-world applications.
Quality Control
UV accelerated weathering testing can be used as part of quality control processes to ensure consistent material performance. It helps manufacturers establish and maintain quality standards, ensuring that their products meet or exceed customer expectations for durability and weathering resistance.
The UV accelerated weathering test chamber works by subjecting the material to intense UV radiation, which is the most damaging component of sunlight, along with controlled temperature and humidity conditions.
The chamber consists of a large, enclosed space with UV lamps installed on the walls or ceiling. These lamps emit high-intensity UV radiation, mainly in the UVA and UVB range, which closely replicates the solar spectrum. The chamber also incorporates a system to control temperature and humidity levels, allowing for the simulation of different weather conditions.
During the test, the material to be evaluated is placed inside the chamber and exposed to the UV radiation for a specified duration. The temperature and humidity conditions can be varied according to the desired test parameters, such as high temperature and high humidity for tropical climates or low temperature and low humidity for arid climates.
The UV radiation causes the material to undergo various degradation processes, such as photochemical reactions, oxidation, and polymer chain scission. These reactions can lead to changes in the material’s physical, chemical, and mechanical properties, including color fading, surface cracking, loss of strength, and degradation of surface coatings.
To evaluate the weather resistance of the material, samples are periodically removed from the chamber at specific time intervals and subjected to various tests and inspections. These tests may include visual examination, color measurement, mechanical testing, chemical analysis, and microscopic analysis.
By exposing the material to accelerated weathering conditions, the UV accelerated weathering test chamber allows for the prediction of long-term performance in a relatively short period of time. The results obtained from these tests help manufacturers, researchers, and quality control personnel to assess the durability, lifespan, and suitability of materials for outdoor applications, such as building materials, automotive components, coatings, and textiles.
1. Temperature Control
Temperature control is very important for ultraviolet light aging test. When irradiated by ultraviolet light, temperature does not participate in the photochemical reaction of the test material, but temperature can affect the rate of light reaction. Generally, The rate of light reaction becomes faster as the temperature increases. Therefore, temperature control also becomes very important when irradiating ultraviolet light. During the UV aging test, the appropriate temperature can be selected according to the intensity of the UV light, and it is generally set between 50°C and 80°C. In addition, the blast system is used to make the temperature distribution in the box more uniform.
2. Ultraviolet Light Irradiation
The main core function of the UV test chamber is ultraviolet light irradiation, which simulates the most harmful ultraviolet light in sunlight. The ultraviolet light content in sunlight is only 7%, but the main factor of degredation in the natural environment is the effect of ultraviolet light. In the aging test, generally only need to simulate the ultraviolet light. When testing the material, the test material needs to be covered by the ultraviolet light in all directions. At present, the ultraviolet light test machine can carry out the full coverage of ultraviolet light.
3. Dew Condensation
The dew condensation function of the UV accelerated weathering tester mainly simulates the dew in the natural environment. In the test chamber, the water in the water sink is heated to generate a large amount of water vapor to keep the humidity in the box at 100%. The high-temperature water vapor condenses on the relatively cold surface of the test sample to produce a condensation effect, which can produce an adverse effect on the test product. In the process of dew condensation, the general test needs to last for 12 hours to see obvious results.
4. Water Spray
The water spray function of the UV accelerated weathering tester is an additional feature that simulates the effects of rain or moisture on the material being tested. It involves the use of a water spray system that sprays water onto the surface of the material during the testing process. The water spray function is typically used in combination with the UV radiation to create a more realistic and comprehensive simulation of outdoor weathering conditions. During the test, water is sprayed onto the material at specific intervals or continuously, depending on the test parameters and requirements.
Both UVA-340 and UVB-313 emit UV lights, but they have different light emission spectrums.
- The luminescence spectrum of the UVA-340 tube ranges from 315nm to 400nm, which is mainly focused on wavelengths 340nm. UVA-340 tube is the optimum choice for simulation of UV in solar light during the noon of summer, which is also recommended in most UV tests.
- The emission spectrum of the UVB-313 tube is in the scope from 280 to 315nm, which is concentrated on wavelengths 313nm. It is much stronger than any spectrum existing in the sunlight on the earth, featuring the maximization of accelerating the weathering during the test, which is beyond the intensity of spectrum existing in a real environment, with harm to specimens.
Polymers and Plastics
This includes polyethylene, polypropylene, PVC, acrylics, polycarbonate, and other plastic formulations. The tester helps assess the resistance of these materials to UV degradation, color fading, embrittlement, cracking, and other forms of deterioration.
Coatings and Paints
The tester evaluates the weathering resistance of coatings and paints applied to various substrates, such as metals, plastics, wood, or concrete. It helps assess the resistance to color fading, chalking, cracking, peeling, gloss loss, and other forms of degradation.
Textiles and Fabrics
UV accelerated weathering testing is utilized to evaluate the durability and colorfastness of textiles and fabrics exposed to outdoor conditions. It helps assess the resistance to fading, degradation, loss of strength, and changes in appearance caused by UV exposure.
Adhesives and Sealants
The tester can assess the weathering resistance of adhesives and sealants used in various applications. It helps evaluate the stability, strength, and durability of these materials when exposed to UV radiation, temperature fluctuations, and other weathering factors.
Automotive Materials
The tester tests materials used in the automotive industry, including interior and exterior components. It includes testing the weathering resistance of materials such as dashboards, seat covers, door panels, exterior trims, and coatings applied to automotive surfaces.
Construction Materials
UV accelerated weathering testing is used to evaluate the durability and weathering resistance of construction materials such as paints, coatings, sealants, roofing materials, window frames, and siding. It helps assess their performance under prolonged exposure to UV radiation, temperature variations, moisture, and other environmental factors.
Aerospace Materials
The tester evaluates the weathering resistance of materials used in aerospace applications. It includes testing the durability of coatings, adhesives, composites, and other materials exposed to high-altitude conditions, extreme temperatures, and UV radiation.
The duration of a UV accelerated weathering test can vary depending on several factors, including the specific test method, the material being tested, and the desired level of accelerated weathering. Generally, accelerated weathering tests aim to simulate the effects of long-term outdoor exposure in a shorter period of time.
Some common test methods, such as ASTM G154 and ISO 4892, specify a specific test duration, typically ranging from a few hundred to several thousand hours. For example, a typical test duration for many polymers and coatings can be around 1000-2000 hours.
However, it’s important to note that the test duration may not directly correspond to the actual time it takes for the material to degrade in real-world outdoor conditions. The purpose of accelerated weathering testing is to accelerate the degradation process and provide a relative comparison between different materials or formulations.
To determine the appropriate test duration, it’s essential to consider the intended application and the expected service life of the material. It can help in selecting a test duration that provides meaningful and relevant results.
It’s also worth mentioning that accelerated weathering tests can be conducted in cycles, involving alternating exposure to UV radiation, moisture, and temperature variations. These cycles can further simulate the complex outdoor weathering conditions and provide a more comprehensive evaluation of material performance.
In summary, the duration of a UV accelerated weathering test can vary depending on the specific test method and material being tested, ranging from a few hundred to several thousand hours. The test duration should be selected based on the intended application and the desired level of accelerated weathering simulation.
UV radiation
The intensity and wavelength of UV radiation can be controlled to simulate different levels of exposure. Generally, either UVA-340 or UVB-313 lamps are utilized.
Temperature
The temperature inside the chamber can be controlled and monitored to simulate the temperature variations experienced in outdoor environments. The temperature can be adjusted to specific levels or follow predefined cycles to replicate seasonal or diurnal temperature changes.
Humidity
The humidity level can be controlled and monitored within the tester to simulate different moisture conditions. This helps evaluate the material’s resistance to moisture-related degradation, such as mold growth, delamination, or dimensional changes.
Irradiance
The irradiance, or the amount of UV radiation reaching the material’s surface, can be measured and controlled. This parameter ensures consistent and accurate exposure levels across different samples or testing conditions.
Exposure Time
The duration of exposure to UV radiation and other weathering factors can be controlled and monitored. This allows for the simulation of long-term outdoor exposure in a shorter period of time, providing accelerated weathering results.
Of course. A UV accelerated weathering tester can simulate different weather conditions by controlling various parameters. While it cannot replicate every aspect of natural weather conditions, it can simulate specific factors that contribute to material degradation. The specific weather conditions available are as below:
UV radiation: Different wavelength and intensity of UV radiation to simulate different levels of exposure are available.
Temperature: The tester can control and vary the temperature inside the chamber to simulate temperature fluctuations experienced in outdoor environments.
Humidity: The humidity level inside the tester can be controlled to simulate different moisture conditions.
Rainfall: While a UV accelerated weathering tester cannot simulate actual rainfall, it can incorporate water spray systems to simulate the effects of rain. These systems can be used to evaluate the material’s resistance to water penetration, surface erosion, or staining.
Condensation: it has the capability to create condensation cycles to simulate the effects of dew or high humidity followed by cooling. This helps assess the material’s resistance to moisture-related issues, such as corrosion, blistering, or peeling.
Request a Quote Now
Please feel free to contact us for more details on the product, price, lead time, payment terms, shipment methods, etc. Amadetech sales specialists will respond within one working day.